Creating circular economies for technology metals
The first industrial revolution saw the use of carbon, iron and steam to create new infrastructures, methods of manufacture and modes of transportation. This carbon-based economy has resulted in climate change and so the latest industrial revolution is seeking to convert our carbon-based world into one based on renewable energy.
The knock on of this is a new reliance on so-called technology metals, which are used for decarbonisation technologies such as lithium ion batteries, fuel cells, photovoltaic devices and supermagnets for wind turbines. These use metals such as rare earth elements, nickel, cobalt, lithium, gold and platinum group metals which are relatively scarce and the amounts required necessitate new technologies for their extraction and recycling. A recent policy commission review of which Professor Andrew Abbott was a commissioner highlighted some of the challenges and recommended solutions to create a circular economy in Technology Metals.
Transport electrification
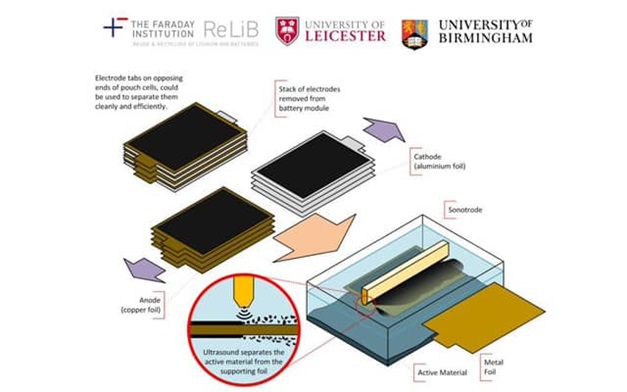
One of the essential strands particularly for electric vehicles is creating reliable lithium ion batteries and establishing an efficient recycling process for the technology metal constituents. By 2040 it is estimated that the lithium ion battery recycling market could be ten times that currently existing for lead acid batteries.
The Leicester team have developed novel recycling technologies for removing valuable metals from the surfaces of the battery electrodes. In a technique similar to that used at the dentist to clean teeth, high powered ultrasound is used to break the active layer from the metal foil. The process is approximately 100 times faster than current technology and produces much purer products.
Professor Abbott is also part of the Faraday Institution’s Recycling of Lithium Ion Battery ReLiB project. In a landmark review in Nature the challenges facing lithium ion batteries were discussed and a recent review has highlighted how changes in battery design could significantly improve not only the ease of recycling but also the economics of the process.
Designer systems for efficient recycling
Professor Abbott explains that recycling metals is traditionally carried out using high temperature molten salts or harsh mineral acids.
He says, “In contrast to traditional methods the Leicester team have discovered a low cost and tuneable ambient temperature molten salt which they called Deep Eutectic Solvents (DESs). These salt-based fluids are mixtures of quaternary ammonium salts with simple organic complexants such as urea or glycerol with unique solvent properties. Their melting point is much lower than those of their individual components. DESs are uniquely effective in solubilising compounds that are usually poorly soluble in water whilst remaining unreactive to air and moisture, crucial for industrial uses.”
DESs can be used for a wide variety of processes including metal coating, natural product extraction, soldering fluxes, recycling and mineral extraction and provide more selectivity, increased efficiency and negation of ecotoxicity compared to aqueous processes involving strong acids or bases previously used. Production at scale is simple, cost-effective and uses bulk commodity chemicals.
Using simple eco-compatible catalysts, the Leicester group have been able to selectively etch metals from complex structures such as printed circuit boards and recover metals with high efficiency. These ideas are being exploited in a new project Met4Tech which aims to develop generic recycling techniques for technology metals. The project also works with manufacturers to suggest design criteria which will make recycling easier.
New methods for extraction
“The metals extraction industry is reliant on expensive, antiquated and environmentally damaging methods. Smelting and refinery frequently uses toxic chemicals like cyanide and mercury and produces hazardous by-products including arsenic and sulphuric acid. This major issue is prevalent in gold production.”
The Leicester team were the first to apply electrocatalytic techniques to metal dissolution and recovery, successfully extracting gold using an iodine catalyst and building on this discovery to develop a range of DESs capable of metal extraction from ores.
This discovery initiated a collaboration with Argo Natural Resources to expand and commercialise these novel solutions. Discussing the collaboration, Argo’s CEO was effusive about the global impacts:
“Professor Abbott effectively came up with a way to un-bake a cake; by using ionic salts, to dissolve metals and then extract and separate metals to allow them to be reused… Imagine the possibility-and the value to an ethical market-of mercury-free gold. Countries that have valuable metals resources will welcome non-toxic recovery and less intrusive mine and waste dam design.”
The collaboration has demonstrated that gold can be efficiently extracted from concentrate and recovered from solution at kg scale while avoiding use of cyanide/mercury notorious for their environmental impact and toxicity for miners.
Their novel process provides a consistent, environmentally sustainable three fold improvement in extraction kinetics. Where before, 7,000 litres of water were required per ounce of gold, non-aqueous DESs bring significantly lower impacts for the water table and local environments.