Space Projects and Instrumentation
Space Instrumentation Research
The Space Projects and Instrumentation Group conducts research into the next generation of instrumentation, for space applications and spun-out of space activities for terrestrial applications. Read about these research areas below.
Space Nuclear
The Space Nuclear Power programme at The University of Leicester has been operating for over a decade. In this time, a number of different radioisotope power systems (RPS) have been developed which can provide thermal and electrical power to future space missions.
RPS use the heat generated from the decay of radioisotope materials such as Plutonium and Americium. Plutonium-238 has historically been used to fuel RPS that have powered Mars rovers and missions to the Outer Solar System and beyond. However, Americium-241 is the radioisotope of choice in Europe, and the University is leading the development of RPS technologies that will use Americium-241. Americium-241 provides a near-constant power supply for many decades which is of particular benefit to long duration missions. The Americium-241 can be reprocessed from civil nuclear waste. Engineers and Scientists at the University have designed the cladding, insulation, and housing for the fuel to ensure it can be handled safely, and survive a range of mission failure scenarios.
The smallest RPS that the team are working on is a Radioisotope Heater Unit (RHU). The RHU is small enough to hold in one hand and can be used to heat spacecraft components for a number of years, which is especially important for missions destined for icy moons, deep space, or surviving the harsh 14-day lunar night. The Radioisotope Thermoelectric Generator (RTG) is much larger and weighs around 10 kg. The RTG provides heat to thermoelectrics which converts thermal power to electrical power. The University researchers are collaborating with industry partners to make lightweight and efficient, low-cost thermoelectrics. RTGs are used to power spacecraft subsystems and recharge batteries when there's limited sunlight. The team have also been developing another system called a Radioisotope Stirling Generator (RSG), which uses Stirling engines to convert heat to electricity more efficiently than thermoelectrics. These novel devices have not yet been used to support spaceflight missions. Am-RSG technology has been considered in concept designs for lunar rovers which could provide the electrical power to operate in shadowed craters, and the thermal power to thermally extract water from trapped ices.
The RHU and RTG development has been funded by the European Space Agency as part of the ENDURE programme. The first flight opportunity for this technology will be a RHU on the ESA Rosalind Franklin Mars rover mission, providing critical heat to the lander that will then deploy Europe's first Mars rover.
X-ray optics
The x-ray optics group have been working on multiple X-ray telescope missions since the 1960s. Initially working on Micro-Channel Plate (MCP) detectors, proportional counters and traditional Wolter instruments for sounding rocket experiments and The Einstein Observatory (HEAO 2). With the world class expertise and knowledge gained in MCP detectors and the 1979 paper by J Angel suggesting novel X-ray telescope designs, the group started to investigate imaging optics based on the production of MCPs. The group produced the very first x-ray image from such an optic and proved the possibility of these novel optics. They became known as Micro Pore Optics (MPOs) in order to differentiate them from MCPs.
The first leader of the group was Professor George Fraser who was instrumental in designing and furthering the use of MPOs for X-ray telescope missions. By tessellating multiple MPOs over a metal frame, it is possible to produce a large field of view optic which would work in a similar way to lobster’s eyes. The first mission to be selected to use a lobster eye telescope was the European Space Agency's (ESA) BepiColombo mission to Mercury. The Mercury Imaging X-ray Spectrometer (MIXS) was the first telescope to use MPOs and created two separate channels by using the optics in one case in a Wolter approximation and the other as a large field of view collimator.
Since BepiColombo (launched October 2018), several missions have been proposed and built using MPOs as their basis. The missions the group has been involved in include; Einstein Probe (launched January 2024), SVOM (launched June 2024), SMILE (due for launch late 2025) and THESEUS (Phase A study), along with several other proposals. The x-ray optics group has been at the forefront of the research in to these optics since their conception and are known as world experts in this area.
UKSA Emerging Technology - Synchrotron Beamline
We have developed technology to allow Mars Sample Return drill cores to be analysed at a synchrotron beamline, whilst maintaining the necessary levels of planetary protection containment. This was funded by a UK Space Agency Emerging Technology-funded grant.
The image shows an experiment at Beamline I12, Diamond Light Source, with an intense X-ray beam shone through fused silica windows and contained drill core of Mars analogue. This allows X-ray diffraction mineralogical data to be obtained, and hence the mineralogy of the sample, but without breaking containment.
Ultra-Precision Surfaces
The Ultra-Precision Surfaces (UPS) research group, now at Space Park Leicester (SPL), has over 30 years of experience in optical manufacturing and surface metrology, serving both astronomical and industrial applications. Why the move to SPL? Because it provides access to highly knowledgeable people and important diagnostic instrumentation, and a fertile environment for developing links with potential end-users of research outputs.
Originally founded by Professor David Walker, the group has led a host of prestigious research projects, and maintains strong collaborations with industry and science-base partners. When the group was previously located at OpTIC in North Wales, an RCUK Basic Technology program established optical manufacturing capability, which led to producing prototype 1.4m hexagonal aspheric mirror segments under contract for the 39 metre ESO European Extremely Large Telescope project. Indeed, much of the background expertise deployed at SPL today stemmed from the above projects, and it is a mark of success that OpTIC itself has developed as a successful commercial enterprise.
At SPL, the UPS group has established an advanced optical manufacturing research facility, operated by Zeeko (a 25-year-old company based in Coalville Leicestershire), in collaboration with SPL. Equipment includes Zeeko CNC polishing machines and Fanuc robot platforms under Zeeko software control. Together, these deliver processes for regular and complex surfaces, ranging from the relatively aggressive Shape Adaptive Grinding (SAG) through to fine polishing. Such processes are iterative in nature, requiring metrology to close the process-loop and assert final surface-quality. With this in view, the laboratory has access to interferometric and scanning profilometric instruments for measuring overall surface form, mid spatial frequencies (‘ripples’) and texture (‘roughness’). With a vision to advance manufacturing technologies for space applications and beyond, the group continues to foster strong partnerships across industry and to build international collaboration.
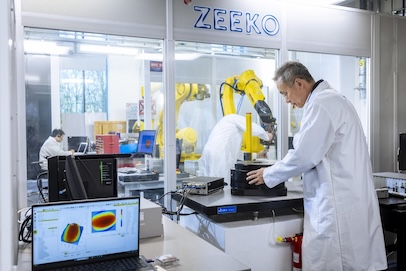
In particular, the UPS group has been awarded the Super-polished Freeform Optical Systems (SFOS) project. This is funded by the Eureka SMART program, is led by Zeeko Ltd, and brings together SPL and the University of Leicester, with Thin Metal Films Ltd, and Swiss academic and industry partners. The primary objective is to develop superior processes and metrology to deliver complex ‘freeform’ optics of unprecedented quality. Specifically, the goal is to achieve 5-10nm form-accuracies and below 0.5nm texture, and capable of withstanding very high laser powers. The central theme is that, by using freeforms, optical systems can be simplified and made more compact, as compared with today’s use of more regular surfaces. The key driver is energy generation by inertial confinement (‘laser fusion’), but with a strong emphasis on exploiting results in other sectors, particularly Space instrumentation.